Plastic extrusion for streamlined, scalable manufacturing solutions
Plastic extrusion for streamlined, scalable manufacturing solutions
Blog Article
A Comprehensive Guide to the Process and Benefits of Plastic Extrusion
In the huge world of manufacturing, plastic extrusion arises as a vital and highly effective procedure. Altering raw plastic right into continuous accounts, it deals with a variety of industries with its exceptional versatility. This overview intends to elucidate the detailed steps associated with this approach, the types of plastic suitable for extrusion, and the game-changing advantages it brings to the industry. The taking place conversation promises to unfold the real-world effects of this transformative procedure.
Understanding the Basics of Plastic Extrusion
While it may appear facility at initial glimpse, the process of plastic extrusion is fundamentally straightforward. The procedure begins with the feeding of plastic material, in the kind of powders, pellets, or granules, into a heated barrel. The designed plastic is then cooled, solidified, and cut right into desired lengths, finishing the procedure.
The Technical Refine of Plastic Extrusion Explained
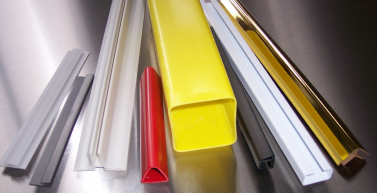
Sorts Of Plastic Suitable for Extrusion
The choice of the appropriate kind of plastic is a vital aspect of the extrusion process. Different plastics use distinct residential properties, making them much more suited to certain applications. Polyethylene, for example, is generally utilized because of its reduced price and simple formability. It offers excellent resistance to chemicals and wetness, making it optimal for items like tubing and containers. Polypropylene is an additional prominent option due to its high melting point and resistance to tiredness. For even more robust applications, polystyrene and PVC (polyvinyl chloride) are frequently picked for their strength and durability. Although these are common alternatives, the selection eventually depends on the particular needs of the item being created. Recognizing these plastic types can significantly boost the extrusion procedure.
Comparing Plastic Extrusion to Various Other Plastic Forming Techniques
Understanding the types of plastic suitable for extrusion paves the means for a broader discussion on exactly how plastic extrusion piles up versus various other plastic developing methods. Plastic extrusion is unrivaled when it comes to producing constant accounts, such as gaskets, pipes, and seals. It also enables for a consistent cross-section along the length of the product.
Secret Advantages of Plastic Extrusion in Production
In the world of manufacturing, plastic extrusion supplies lots of substantial advantages. One significant benefit next is the cost-effectiveness of the process, which makes it a financially enticing production technique. Additionally, this technique gives premium item versatility and improved production speed, therefore raising overall manufacturing efficiency.
Affordable Manufacturing Approach
Plastic extrusion leaps to the center as a cost-efficient manufacturing approach in production. This process stands apart for its capacity to create high volumes of material rapidly and effectively, providing manufacturers with substantial cost savings. The key price benefit is the capacity to make use of cheaper basic materials. Extrusion makes use of thermoplastic materials, which are much less expensive compared to steels or porcelains. Further, the extrusion process itself is reasonably easy, reducing labor prices. Furthermore, plastic extrusion needs much less power than conventional manufacturing approaches, contributing to lower functional costs. The process likewise minimizes waste, as any kind of defective or excess materials can be reused and recycled, providing another layer of cost-effectiveness. Overall, the financial benefits make plastic extrusion a highly attractive alternative in the production market.
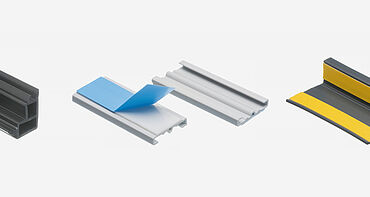
Superior Item Versatility
Past the cost-effectiveness of plastic extrusion, another significant benefit in manufacturing lies in its exceptional product adaptability. This makes plastic extrusion a suitable service for industries that require tailored plastic elements, such as vehicle, building, and packaging. In essence, plastic extrusion's product adaptability promotes technology while enhancing operational effectiveness.
Boosted Manufacturing Speed
A considerable advantage of plastic extrusion depends on its boosted production speed. This manufacturing process permits high-volume production in a reasonably short time span. It can creating long, continual plastic accounts, which considerably reduces the production time. This review high-speed manufacturing is specifically advantageous in industries where large amounts of plastic parts are required within tight deadlines. Couple of other production processes can match the rate of plastic extrusion. Furthermore, the capability to preserve constant high-speed production without giving up item quality establishes plastic extrusion in addition to various other techniques. The enhanced manufacturing rate, as a result, not only allows producers to meet high-demand orders yet additionally contributes to enhanced efficiency and cost-effectiveness. This beneficial attribute of plastic extrusion has made it a preferred choice in countless markets.
Real-world Applications and Influences of Plastic Extrusion
In the realm of production, the technique of plastic extrusion holds extensive value. The financial advantage of plastic extrusion, largely its cost-efficient and high-volume outcome, has actually changed manufacturing. The industry is persistently striving for advancements in recyclable and eco-friendly materials, indicating a future where the advantages of plastic extrusion can be preserved without jeopardizing environmental sustainability.
Final thought
In verdict, plastic extrusion is a extremely efficient and efficient method of transforming resources right into varied products. It uses numerous benefits over various other plastic developing approaches, including cost-effectiveness, high result, marginal waste, and design flexibility. Its impact is exceptionally really felt in various markets such as building, vehicle, and durable goods, making it a critical process in today's manufacturing landscape.
Digging deeper into the technical procedure of plastic extrusion, it starts with the option of the suitable plastic product. As soon as cooled, the plastic is reduced right into the required sizes or wound onto reels if the product is a plastic film or sheet - plastic extrusion. Comparing Plastic Extrusion to Other Plastic Forming Approaches
Recognizing the types of plastic suitable for extrusion paves the means for a wider conversation on how plastic extrusion stacks up versus other plastic creating methods. Few various other production processes can match the speed informative post of plastic extrusion.
Report this page